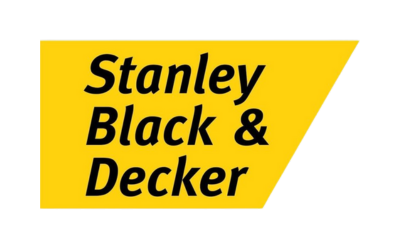
The client
Stanley Black and Decker
The longstanding partnership between Stanley Black & Decker and PDMS began in 1998 when we developed their Bill of Material (BOM) system. This system was used to maintain a detailed record of all Stanley Black & Decker products and parts, technical and safety information, repair, and service instructions, and more.
The system’s purpose was to support the Technical Service teams and provide Service Support to ‘on-the-ground’ service and repair agents who perform the warranty and repair of tools and equipment sold by Stanley Black & Decker. The scale of the system is significant, as Stanley Black & Decker maintain over 100,000 different product revisions and over 500,000 parts for over 30 brands which are distributed across the globe. In addition, product lifespans can be as great as ten years, plus a five-year service life which means the process for maintaining repair information is highly complex.
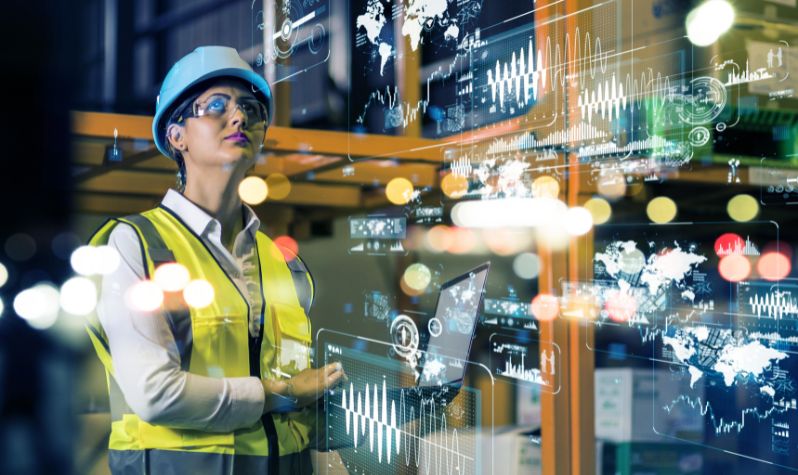
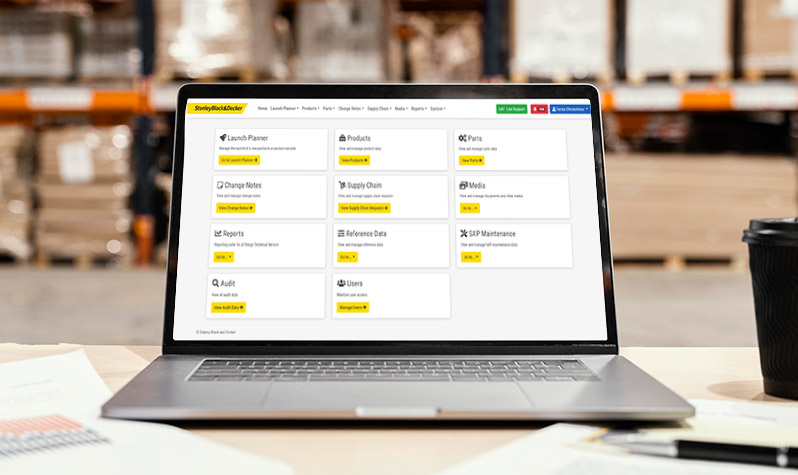
The project
Using an Agile approach to development, PDMS worked closely with Stanley Black & Decker to ensure regular feedback and eliminate risk early. The agile approach also allowed the team to address the project in manageable units, enabling the team to focus on high-quality development, testing, and collaboration.
The development process included a discovery phase, early prototypes, development spikes, sprint cycles, and regular releases, demonstrations and testing. The system was built using the Microsoft stack, ensuring strong support and security. GSIS also integrates with several other systems including their SAP ERP for inventory accounting, automating parts management in warehousing, and introducing new workflows for the supply chain team.
The results
Futureproofed platform with improved performance
GSIS brought about a significant number of benefits and improvements for SBD. It dramatically improved the user experience, offering a modern browser-based interface with the SBD brand and familiar terminology, consistency, and responsiveness. Features such as shortcuts, cues, and wizards help users complete tasks efficiently as well as usability incorporated into the design process so users can easily recognise usage patterns and learn to use the new system quickly.
As a web-based system, GSIS eliminated the need for desktop installations, improving flexibility and security. Performance and efficiency were also improved, managing over eight million records and two million transactions with faster response times.
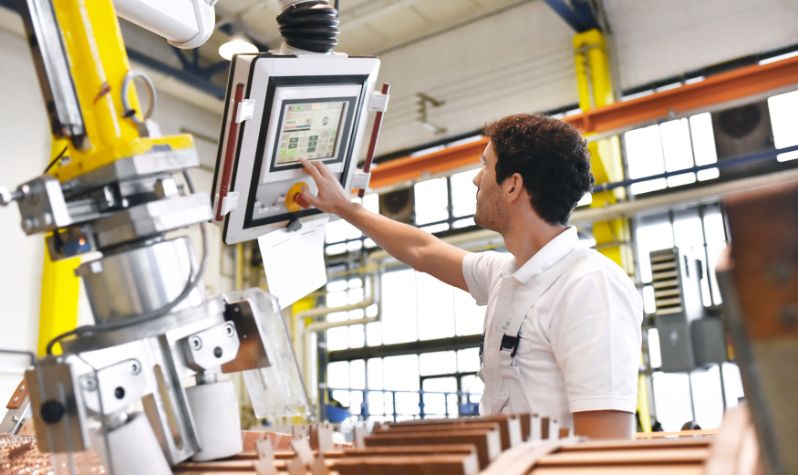
Statistics
What next?
We are now in the continuous improvement stage of the project and work with Stanley Black and Decker on an ongoing support basis to drive further efficiencies and value.
Stanley Black & Decker are looking at driving further value to the business from the solid foundation GSIS provides as a single data source for products and parts. The possibilities provided by excellent data design from the outset can be far reaching throughout an organisation and can assist many other departments including sales, marketing, and accounting.
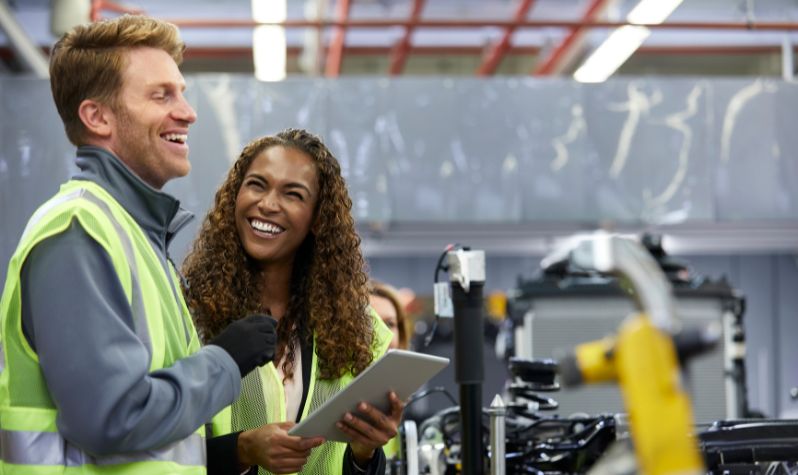
More case studies

Unlocking the hidden value in a legacy ERP system
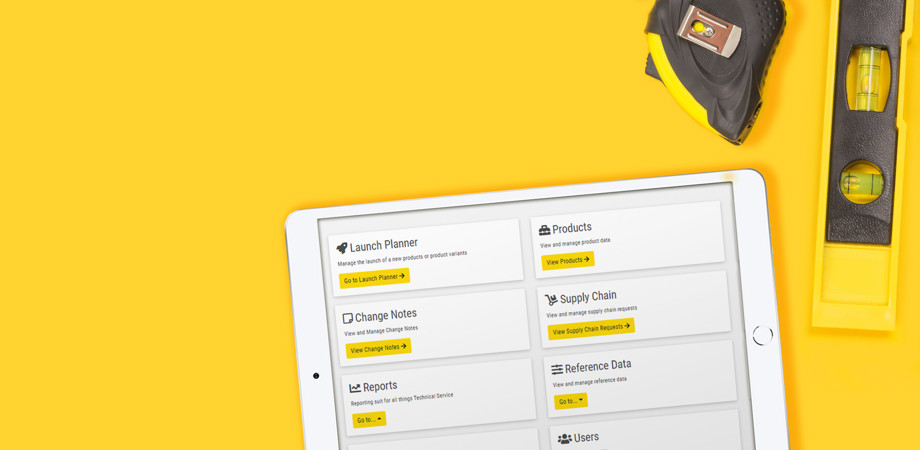
Pioneering a global process for a household name
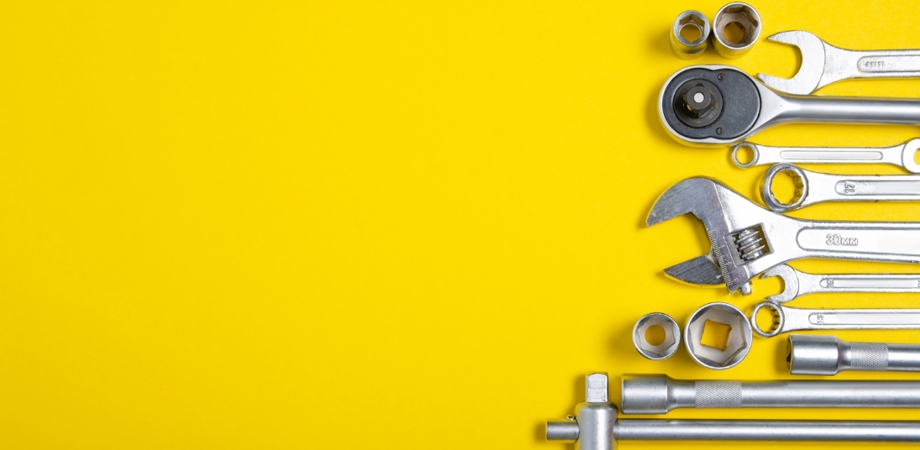